Avoiding Pressure Relief Problems Chemical Engineering©
Department Editor: Scott Jenkins
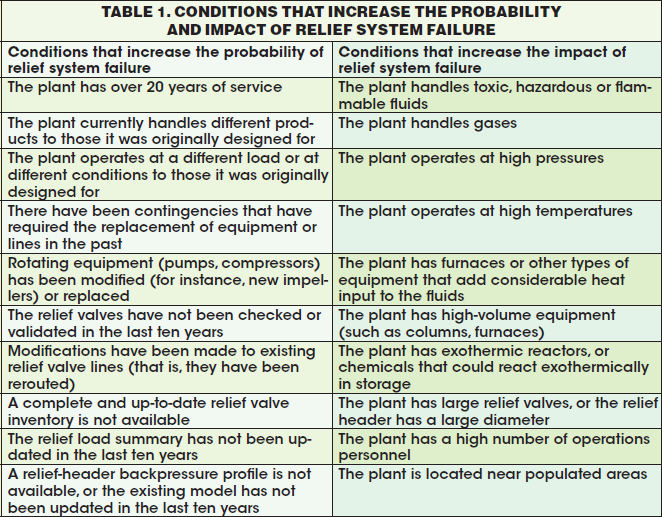
Pressure relief valves and rupture disks are critical safety devices for protecting personnel and processing equipment from overpressurization situations. Presented here are several engineering practices that can help to identify and address common problems with the pressure relief systems of chemical process industries (CPI) facilities.
Common causes of overpressurization
Overpressure situations can have a variety of causes. Here are some common situations that may cause increased pressure in processing facilities. Each potential cause is followed by one or more factors that contribute to the overpressure.
Overpressure situations can have a variety of causes. Here are some common situations that may cause increased pressure in processing facilities. Each potential cause is followed by one or more factors that contribute to the overpressure.
- External fire: Potential vapors from the fire must be relieved with a safety valve on the vessel
- Blocked outlets: Blocked outlets can be caused by control valve failure, inadvertent valve operation and others
- Utility failure: General or partial power failure, loss of instrument air, cooling water, steam, fuel gas or fuel oil
- Loss of cooling duty: Loss of quench steam, air-cooled exchanger failure, loss of cold feed or loss of reflux
- Thermal expansion: External heat can cause liquid volume to rise in fluids that are blocked in a vessel or pipeline
- Abnormal heat input: Increased supply of fuel gas, or faster heat transfer after exchanger revamp, and others
- Abnormal vapor input: Failure of upstream control valve to fully open, or inadvertent valve opening
- Loss of absorbent flow: Interruption of absorbent flow when gas removal by absorbent is more than 25% of total inputvapor flow
- Entrance of volatile materials: Ingress of volatile liquid into hot oil in a process upset
- Accumulating noncondensibles: Blocking of noncondensible vent
- Valve malfunction: Human error or checkvalve malfunction, resulting in backflow, control valve failure
- Process control failure: Failure of distributed control systems (DCS) or programmable logic controller (PLC)
Valves
To avoid problems with pressure relief systems, plant managers should consider these
practical guidelines.
Assess risk. Many factors can increase the risk and impact of pressure-relief-system failure. If several of the conditions in Table 1 apply, plant managers should consider planning a detailed study of the pressure relief systems, such as a quantitative risk analysis (QRA) or a relief-system validation study.
Maintain up-to-date relief-valve data. Plant managers should maintain accurate and
up-to-date relief-valve data, including relief valve inventory, relief-valve load summary and relief-header backpressure profile. The inventory is a list of basic information that applies to each valve, such as process unit, location, discharge location, connection sizes, orifice size, manufacturer, model, installation date, and date of last inspection.
The loads summary contains all the overpressure scenarios and relief loads for each device at the plant. The backpressure profile of the pressure-relief network is valuable when evaluating the critical contingencies of the systems, as it can be used to identify relief valves operating above their backpressure limits.
Relief-system study. A relief-system validation study comprises three phases:
To avoid problems with pressure relief systems, plant managers should consider these
practical guidelines.
Assess risk. Many factors can increase the risk and impact of pressure-relief-system failure. If several of the conditions in Table 1 apply, plant managers should consider planning a detailed study of the pressure relief systems, such as a quantitative risk analysis (QRA) or a relief-system validation study.
Maintain up-to-date relief-valve data. Plant managers should maintain accurate and
up-to-date relief-valve data, including relief valve inventory, relief-valve load summary and relief-header backpressure profile. The inventory is a list of basic information that applies to each valve, such as process unit, location, discharge location, connection sizes, orifice size, manufacturer, model, installation date, and date of last inspection.
The loads summary contains all the overpressure scenarios and relief loads for each device at the plant. The backpressure profile of the pressure-relief network is valuable when evaluating the critical contingencies of the systems, as it can be used to identify relief valves operating above their backpressure limits.
Relief-system study. A relief-system validation study comprises three phases:
- survey and information gathering
- modeling of the existing relief system and
- relief system troubleshooting
Modeling. Results from accurate modeling can identify the need for replacement of a relief valve. However, developing an accurate model for every relief valve in a plant is costly and impractical. A compromise that minimizes time and effort while targeting potential problem areas is to verify each system starting from a simple model with conservative assumptions, and to develop more accurate models only for those items that do not comply with the required parameters under the original assumptions. See Ref. 1 for an example.
Rupture Disks
Rupture disks are often installed as the last line of defense against overpressurization.
When handled and installed properly, rupture disks are a safe and economical way to protect personnel and process equipment.
To help avoid problems with rupture disks, consider the following guidelines:
Evaluate pressure measurement. Since most rupture disks react to overpressure within milliseconds, it is important to sample and measure the pressure near the rupture disk, and at time intervals that are narrow enough to catch rapid pressure spikes.
Evaluate fatigue and corrosion of disks. Process engineers should pay attention to the effects of corrosion and fatigue on the performance of rupture disks. In some cases, rupture disks are operating at up to 95% of their rated burst pressure.
And rupture disks can have thicknesses of 0.001 in. If a change in material thickness occurs because of corrosion or changes in operating pressure occur, failures can occur.
Check installation. As precision devices, rupture disks have tight burst tolerances. Because of this, it is critical that the rupture disk be installed correctly, with attention to torque, position and possible inadvertent damage to seating surfaces. See Ref. 2 for features that aid installation.
Check process temperature. The strength of the materials used to manufacture rupture disks is always dependent upon the temperature. It is important that rupturedisk burst pressures are specified for the temperature at which they will operate. It is important to keep in mind that it is possible that the specified burst pressure may not be the same as the temperature inside the vessel, especially if the vessel is insulated.
References
1. Giardinella, S. Aging Relief Systems — Are they working properly? Chem. Eng., July 2010, pp. 38–43.
2. Wilson, A.T. Troubleshooting Field Failures of Rupture Disks. Chem Eng. December 2006, pp. 34–36.
3. Wong, W., Protect Plants Against Overpressure. Chem Eng., June 2001, pp. 66–73.
Rupture Disks
Rupture disks are often installed as the last line of defense against overpressurization.
When handled and installed properly, rupture disks are a safe and economical way to protect personnel and process equipment.
To help avoid problems with rupture disks, consider the following guidelines:
Evaluate pressure measurement. Since most rupture disks react to overpressure within milliseconds, it is important to sample and measure the pressure near the rupture disk, and at time intervals that are narrow enough to catch rapid pressure spikes.
Evaluate fatigue and corrosion of disks. Process engineers should pay attention to the effects of corrosion and fatigue on the performance of rupture disks. In some cases, rupture disks are operating at up to 95% of their rated burst pressure.
And rupture disks can have thicknesses of 0.001 in. If a change in material thickness occurs because of corrosion or changes in operating pressure occur, failures can occur.
Check installation. As precision devices, rupture disks have tight burst tolerances. Because of this, it is critical that the rupture disk be installed correctly, with attention to torque, position and possible inadvertent damage to seating surfaces. See Ref. 2 for features that aid installation.
Check process temperature. The strength of the materials used to manufacture rupture disks is always dependent upon the temperature. It is important that rupturedisk burst pressures are specified for the temperature at which they will operate. It is important to keep in mind that it is possible that the specified burst pressure may not be the same as the temperature inside the vessel, especially if the vessel is insulated.
References
1. Giardinella, S. Aging Relief Systems — Are they working properly? Chem. Eng., July 2010, pp. 38–43.
2. Wilson, A.T. Troubleshooting Field Failures of Rupture Disks. Chem Eng. December 2006, pp. 34–36.
3. Wong, W., Protect Plants Against Overpressure. Chem Eng., June 2001, pp. 66–73.
1 comentario:
temperature relief valve for hvac
Publicar un comentario
Bienvenido a Avibert.
Deja habilitado el acceso a tu perfil o indica un enlace a tu blog o sitio, para que la comunicación sea mas fluida.
Saludos y gracias por comentar!