Infrared Temperature Measurement Department Editor: Scott Jenkins
Chemical Engineering©

Contact-based temperature sensors, such as thermocouples and resistance temperature detectors (RTDs), have demonstrated accurate and cost-effective operation throughout the chemical process industries (CPI). However, there are many applications and settings where they are simply not practical. In those cases, engineers can turn to a host of non-contact temperature measurement devices, many of which are based on measuring infrared (IR) radiation. IR thermometers can routinely perform measurements in situations where readings with contact thermometers would be virtually impossible. Situations where IR-based temperature measurement should be considered include the following:
- Rapid and frequent temperature readings are required
- Objects are moving
- Objects are within strong electromagnetic fields, such as in processes involving induction or microwave heating
- Rapid thermal changes are the norm
- Objects needing measurement are located in process chambers or behind windows
- The surface temperature of an object or equipment requires measurement
- Locations are inaccessible to contact thermometers
- Areas to be measured would be damaged or contaminated by contact measurement
- Varying surface-temperature distributions are present
- Objects are made from materials with low heat capacity and low thermal conductivity
- Materials to be measured are gaseous, such as combustion gases and flames
Within the CPI, IR thermometry is most effective and used most frequently in semiconductor and wafer processing, cement and lime processing, rotating kiln shells, waste incineration, glass processing, sintering and heat treating, metals processing and drying applications. While IR thermometers are generally more expensive than contact thermometers, they usually have longer lifetimes and require less maintenance.
A general knowledge of the key aspects of thermal radiation physics can help users apply and operate the devices more effectively.
Stefan-Boltzmann law
The energy radiated by an object per unit surface area per unit time is related to its temperature by the Stefan-Boltzmann law, which states that irradiance (in J/s/m2) is proportional to the fourth power of the object’s temperature multiplied by its emissivity. A constant of proportionality (the Stefan-Boltzmann constant) is required for calculations.
In a perfect (theoretical) blackbody radiator, emissivity equals one.
A general knowledge of the key aspects of thermal radiation physics can help users apply and operate the devices more effectively.
Stefan-Boltzmann law
The energy radiated by an object per unit surface area per unit time is related to its temperature by the Stefan-Boltzmann law, which states that irradiance (in J/s/m2) is proportional to the fourth power of the object’s temperature multiplied by its emissivity. A constant of proportionality (the Stefan-Boltzmann constant) is required for calculations.
In a perfect (theoretical) blackbody radiator, emissivity equals one.
Operation
Most IR thermometers operate according to the same basic operating principles (Figure 1).
A bandwidth ilter and optical lens are used to focus the IR energy emitted by an object onto a detector, which converts the IR radiation into an electrical signal. After compensating for emissivity (see below) and ambient temperature, an analog output is generated to provide temperature measurement. The analog signal can be converted to digital when fast acquisition rates are required.
Emissivity
The emission of thermal radiation is a surface phenomenon for most materials. The term emissivity refers to an object’s ability to emit thermal radiation.
Emissivity is defined as the ratio between the energy emitted by an object at a given temperature and a perfect radiator, or blackbody, at the same temperature. Emissivity values lie between zero and one. IR thermometers generally have the ability to compensate for the different emissivity values of materials.
Materials with the highest emissivity values are the easiest to measure accurately with IR thermometers, while those with low emissivities are more difficult. For example, some polished, shiny metallic surfaces, such as aluminum, are so reflective in the infrared that accurate temperature measurement is not always possible.

Tables listing emissivity values for various materials have been published, and are available for reference (Table). Some IR thermometers allow users to change emissivity values according to the material being measured, while others have a pre-set emissivity value.
When using IR thermometry, it is important to consider that materials can have different emissivity values at different wavelengths. To determine an emissivity value, you can heat a material to a known temperature, then adjust the emissivity value of the instrument until the IR thermometer matches the known temperature.
Field of view (FOV)
The FOV is the angle of vision at which the instrument operates and is determined by the optics of the system. The optical system of the IR thermometer collects the IR energy from a circular measurement spot, and focuses the energy on the detector. The optical resolution of the instrument is determined by the ratio between the distance from instrument to object and the size of the spot being measured (distance-to-spot ratio). Higher ratios mean better resolution.
Ideally, the target being measured should fill the instrument’s FOV. For the best performance, the target object area should exceed the FOV by a factor of about 1.5 (Figure 2).
Calibration
IR thermometers can be calibrated by aiming at blackbody radiators that are designed specifically for calibration and testing. By varying the source temperature of the blackbody, calibrators can tune the IR sensor’s internal measurement signal to known temperatures.
Selection questions to consider
When selecting an IR thermometer for a CPI application, it is important to consider the following questions:
1. Young, A., IR Thermometry Finds CPI Niches, Chem. Eng., Feb. 2002, pp. 56–60.
2. Omega Engineering Inc. [Internet]. c2003–2010. Stamford (CT). [cited Feb. 2011]. Available from: http://www.omega.com/.
Most IR thermometers operate according to the same basic operating principles (Figure 1).
A bandwidth ilter and optical lens are used to focus the IR energy emitted by an object onto a detector, which converts the IR radiation into an electrical signal. After compensating for emissivity (see below) and ambient temperature, an analog output is generated to provide temperature measurement. The analog signal can be converted to digital when fast acquisition rates are required.
Emissivity
The emission of thermal radiation is a surface phenomenon for most materials. The term emissivity refers to an object’s ability to emit thermal radiation.
Emissivity is defined as the ratio between the energy emitted by an object at a given temperature and a perfect radiator, or blackbody, at the same temperature. Emissivity values lie between zero and one. IR thermometers generally have the ability to compensate for the different emissivity values of materials.
Materials with the highest emissivity values are the easiest to measure accurately with IR thermometers, while those with low emissivities are more difficult. For example, some polished, shiny metallic surfaces, such as aluminum, are so reflective in the infrared that accurate temperature measurement is not always possible.

Tables listing emissivity values for various materials have been published, and are available for reference (Table). Some IR thermometers allow users to change emissivity values according to the material being measured, while others have a pre-set emissivity value.
When using IR thermometry, it is important to consider that materials can have different emissivity values at different wavelengths. To determine an emissivity value, you can heat a material to a known temperature, then adjust the emissivity value of the instrument until the IR thermometer matches the known temperature.
Field of view (FOV)
The FOV is the angle of vision at which the instrument operates and is determined by the optics of the system. The optical system of the IR thermometer collects the IR energy from a circular measurement spot, and focuses the energy on the detector. The optical resolution of the instrument is determined by the ratio between the distance from instrument to object and the size of the spot being measured (distance-to-spot ratio). Higher ratios mean better resolution.
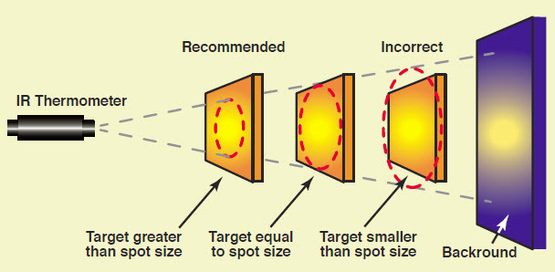
Calibration
IR thermometers can be calibrated by aiming at blackbody radiators that are designed specifically for calibration and testing. By varying the source temperature of the blackbody, calibrators can tune the IR sensor’s internal measurement signal to known temperatures.
Selection questions to consider
When selecting an IR thermometer for a CPI application, it is important to consider the following questions:
- What is the required proximity to the target?
- What is the size of object to be measured, and will it it the instrument’s FOV?
- Are there any physical obstructions between the object to be measured and the measuring device
- Are smoke, dust or other particulate matter likely to be in the measurement area?
- What are the measurement control frequency requirements?
- Does the object have a shiny surface?
- What are the output/interface requirements?
1. Young, A., IR Thermometry Finds CPI Niches, Chem. Eng., Feb. 2002, pp. 56–60.
2. Omega Engineering Inc. [Internet]. c2003–2010. Stamford (CT). [cited Feb. 2011]. Available from: http://www.omega.com/.
1 comentario:
Thanks so much for sharing this. I am going to be using temperature measurement devices for the first time at my upcoming lab, which I am looking forward to. This posting was really helpful in expanding my knowledge before hand.
Publicar un comentario
Bienvenido a Avibert.
Deja habilitado el acceso a tu perfil o indica un enlace a tu blog o sitio, para que la comunicación sea mas fluida.
Saludos y gracias por comentar!